Copper and Brass Comparison
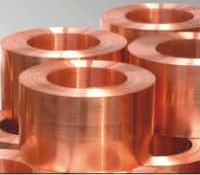
One of our dealers recently asked us to help him explain the differences between copper and brass to his clients and why we use copper as the primary material for our fixtures. We want to share this with our readers to expose a few myths and misconceptions about which material is best for outdoor landscape lighting. This may be a lengthy read but hopefully you will find the information useful.
When comparing copper to brass luminaires, both materials are good choices for the fixture composition but copper offers a few key advantages over brass. Remember, brass is a composite typically comprised of copper and zinc (usually about 70% copper and 30% zinc). The zinc provides hardness to the alloy which makes brass an excellent choice for parts where the softer copper is not suitable for such applications as screws and knuckles. Obviously, when you have 70% of the brass makeup costing say $6800 per tonne and 30% of the makeup costing $1835 per tonne (current prices on the LME on 10/5/11), brass should naturally be a less expensive material than 100% copper. The two primary reasons brass is used in products are, 1) certain applications need harder materials such as mentioned earlier with screws for example. 2) brass can be polished to a beautiful finish for lamps, doorknobs, etc. and the zinc helps resist tarnishing, especially important for indoor lighting fixtures and decorative hardware.
Now for the good stuff. There are 2 very meaningful advantages I discuss with my clients locally which seem to be important to these homeowners.
First, copper is one of the few materials that will truly stand the test of time, which is one reason why copper is used for roofing, plumbing, and historic structures that have been around for years (think of the statue of liberty). The information below provides a little insight to this but the real difference between copper and brass is in the last section regarding the effects of corrosion.
Copper and copper alloys provide superior service in many of the applications included in the following general classifications:
- Applications requiring resistance to atmospheric exposure, such as roofing and other architectural uses, hardware, building fronts, grille work, hand rails, lock bodies, doorknobs, and kick plates
- Freshwater supply lines and plumbing fittings, for which superior resistance to corrosion by various types of waters and soils is important
- Marine applications – most often freshwater and seawater supply lines, heat exchangers, condensers, shafting, valve stems, and marine hardware – in which resistance to seawater, hydrated salt deposits, and biofouling from marine organisms is important
- Heat exchangers and condensers in marine service, steam power plants, and chemical process applications, as well as liquid-to-gas or gas-to-gas heat exchangers in which either process stream may contain a corrosive contaminant
- Industrial and chemical plant process equipment involving exposure to a wide variety of organic and inorganic chemicals
- Electrical wiring, hardware, and connectors; printed circuit boards; and electronic applications that require demanding combinations of electrical, thermal, and mechanical properties, such as semiconductor packages, lead frames, and connectors
Effects of alloy compositions on corrosion
Coppers and high-copper alloys (C 10100 – C 19600; C 80100 – C 82800) have similar corrosion resistance.
They have excellent resistance to seawater corrosion and biofouling, but are susceptible to erosion-corrosion at high water velocities. The high-copper alloys are primarily used in applications that require enhanced mechanical performance, often at slightly elevated temperature, with good thermal or electrical conductivity. Processing for increased strength in the high-copper alloys generally improves their resistance to erosion-corrosion.
Brasses (C 20500 – C 28580) are basically copper-zinc alloys and are the most widely used group of copper alloys. The resistance of brasses to corrosion by aqueous solutions does not change markedly as long as the zinc content does not exceed about 15%.
Above 15% Zn, dezincification may occur.
Source: http://www.keytometals.com/article16.htm
As you can see, since most traditional brass composition for our industry has 30% zinc (twice the 15% mentioned above), dezincification will occur over time which depletes the zinc from the material and leaves the remaining part porous and weak. See below from Wikipedia.com
Leaching of Zinc (dezincification)
The most common example is selective leaching of zinc from brass alloys containing more than 15% zinc (dezincification) in presence of oxygen and moisture, eg. from brass taps in chlorine-containing water. It is believed that both copper and zinc gradually dissolved out simultaneously and copper precipitates back from the solution. The material remaining is a copper-rich sponge with poor mechanical properties, and color changed from yellow to red. Dezincification can be caused by water containing sulfur, carbon dioxide and oxygen.
The second advantage of copper over brass (and many other materials used for lighting products) is the true sustainability of the material from an eco-friendly perspective. I say “true” because many companies tout their products as being environmentally friendly and sustainable but if you cut through the chatter and see what sustainable really means, you will see copper is a standout from other materials. Yes, you can technically recycle the plastic and aluminum products but the feasibility of this does not make financial sense. Brass, being an alloy is not as pure a material as copper so copper is the more likely material to end up being recycled … AND the material holds its intrinsic value time after time, a key to true sustainability. In other words, copper at the beginning of the production stage and at the end of the product’s lifespan, will maintain a significant portion of its value, making it desirable and, therefore financially feasible to recycle. This material will truly sustain itself over time.
By the way, there are many types of “brasses” and then you have the “bronze” materials, all of which are alloys or composites (see the link below for more on this). Each has its advantages and disadvantages for certain applications but for landscape lighting, copper is, in my humble opinion, the absolute best choice for the highest quality and affordability in professional lighting. The purity and sustainability of copper, coupled with the beautiful patina finish that naturally occurs over time can’t be beat. Lastly, copper fixtures and LED are a natural combination when considering true environmentally friendly options.
Source: http://en.wikipedia.org/wiki/Brass
Happy Selling!